APSM is excited to announce its software Certification Training Schedule for 2023. The APSM Certification program offers participants credentials through certification and testing in order to recognize depth in competency and expertise in the APSM software suite.
In industrial settings where a missed step can lead to serious consequences, safety can’t be managed by spreadsheets and memory alone. Yet too often, that’s precisely what happens. Safety managers juggle paper forms, separate tracking systems, and disconnected tools to stay on top of their responsibilities. When something gets overlooked, it’s not always evident until it’s too late.
“You can’t fix what you can’t see.” That’s a line we hear often, and it’s the reality for many facilities working under strict OSHA and EPA standards. When data is buried, delayed, or outdated, safety suffers. But now, with the rise of real-time safety dashboards, PSM managers are gaining visibility they never had before. This article shows why these dashboards matter, how they work, and what to look for if you’re ready to simplify your process safety management.
Disconnected Systems, Delayed Decisions
Let’s start with the problem. Many industrial sites use a patchwork of tools to manage safety. There’s one system for training, another for audits, and a third for managing SOPs. Often, the real system is a collection of spreadsheets, calendars, and inboxes, each managed by a different person.
Tyson Alexander from APSM described a customer experience well in a recent podcast. “Before, I spent 16 hours a week just gathering that information so that I could make a report.” That’s two full workdays, and that’s not uncommon. When time is spent chasing data instead of managing safety, the whole program suffers.
The burden falls on managers to chase down data, confirm it’s current, and stitch it into something usable. There’s no room for error, yet the setup practically guarantees it. And when someone leaves, like a maintenance manager or safety lead, it’s even harder to tell what’s been done and what’s been missed.
When safety tasks live in different places and rely on different people to connect the dots, visibility disappears, and with it, control. That’s where dashboards come in.
Why PSM Managers Need Real-Time Dashboards
A real-time safety dashboard is a centralized, digital tool that gives you live updates on your entire process safety program. It tracks tasks, highlights overdue items, and flags what needs attention, all in one place. By pulling data from every part of your PSM system, training, documentation, PHAs, SOP reviews, audits, and more, it keeps everything connected and current.
It’s not just for management. Operators see what’s on their plate. Supervisors get a view of their team’s progress. Corporate leaders see how each site is performing. You’re not just reviewing records, you’re seeing what’s happening, as it happens. That kind of visibility helps make sure your systems are running the way they’re supposed to.
That includes:
- Tracking open action items from PHAs and audits
- Seeing which training is overdue
- Checking the status of MOCs
- Confirming when SOPs need review
- Monitoring compliance timelines and managing approvals
Without a dashboard, you might have to dig through folders or email chains to answer a simple question like, “When was this last reviewed?” With a dashboard, that answer is right in front of you, and during audits or inspections, that makes all the difference. But not all dashboards are created equal. To truly improve safety performance, the right features have to be in place.

What Makes a Good Dashboard?
A good safety dashboard doesn’t just display data, it drives decisions. It helps the right people focus on the right tasks at the right time. That’s the difference between checking a box and actually managing risk.
- Role-based views: Operators see their daily tasks, keeping their focus clear and manageable. Managers and safety leads get high-level visibility into trends, overdue items, and site performance, all without digging through layers of data. Customized views reduce noise and help every team member zero in on what matters most to them.
- Smart alerts: Notifications flag important issues before they’re missed. Whether it’s an expired certification, an open investigation, or a delayed approval, alerts keep teams one step ahead of potential compliance gaps. In industries with seasonal staff or rotating shifts, like food processing or cold storage, these alerts help fill the cracks that human memory often misses.
- Task generation: When a procedure changes, related training tasks are triggered automatically. This closes the gap between documentation and action. It also ensures that compliance updates don’t rely on email reminders or memory. In practice, it means operators are trained on the latest procedures before they hit the floor.
- Linked workflows: A PHA recommendation can drive updates to SOPs, which then prompt new training assignments, which could also drive the required approval from a manager. The dashboard connects these steps automatically, maintaining a clear chain of accountability. Without this integration, safety tasks often stall out or get lost in disconnected systems.
These aren’t just features, they’re what help you stay ahead of problems instead of reacting after the fact. That kind of clarity builds confidence across the team. It’s exactly what inspired APSM to create a tool that fits the pace and pressure of real-world operations.
APSM’s Action Center: Real-Time Visibility That Works
At APSM, we didn’t build our tools in a vacuum, we built them from experience. Our Action Center is more than a dashboard. It’s a control center for PSM teams managing the daily demands of safety, training, and compliance across complex operations.
“It’s a full-fledged PSM management system,” said Tyson Alexander of APSM. “The Action Center gives you eyes on every open action, all in one place.” That includes overdue training, pending approvals, and time-sensitive tasks, clearly organized and assigned by role. When you log in, you don’t have to dig. You see exactly what needs your attention.
And for large operations, the payoff is even greater. One corporate PSM manager responsible for 200 sites used to spend hours each week just gathering updates. Now? “It’s not even a press-the-button. It’s an automated report. It just shows up in her inbox.” That’s what real-time visibility delivers: less guesswork, more control, and time back for what matters.
Ready to Get Ahead of Compliance?
APSM offers two powerful, connected tools:
- APSM Portal: Our classic software package for managing your PSM and RMP programs
- APSM Catalyst: Our most flexible and customizable PSM Management System – complete with CMMS tools and API integrations for maximum control.
Our system is modular. Start with what you need, like Document Management, SOPs or PHAs, and expand as you grow. Whether you manage one site or hundreds, APSM gives you a clear view of your program and the tools to keep it running safely.
Can you see the full status of your PSM program right now? If not, we’re here to help. Visit APSM to learn more or schedule a demo today.
Listen to Tyson Alexander’s Story on the “Amplify Your Process Safety” Podcast
In a recent episode of the Amplify Your Process Safety podcast, APSM’s Tyson Alexander shares how their software solution evolved from a simple need to a powerful platform trusted by facilities across the country.
“You shouldn’t be scrambling if OSHA shows up. You should be able to log in and know exactly where you stand,” says Tyson. “That’s what APSM gives you — confidence and control over your PSM.”
Built to manage every element of PSM — from PHAs and SOPs to MOCs and training — APSM offers an all-in-one, cloud-based system designed to keep your facility audit-ready, safe, and organized.
With customizable workflows, real-time dashboards, and modular tools, APSM works for small teams and large enterprises alike. Whether you’re replacing spreadsheets or uniting six disconnected tools, APSM makes managing process safety easier and more effective.
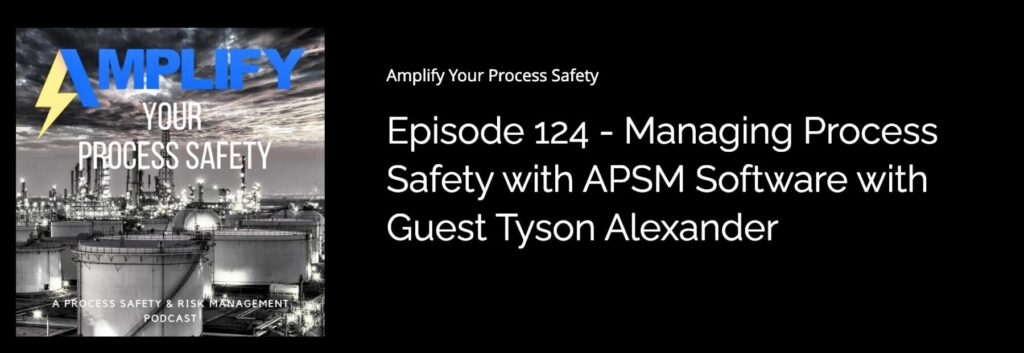
Click here for more ways to listen.
What You’ll Hear About
- How APSM started with a vision — and a dial-up modem!
- Why managing all your PSM data in one place changes the game
- How facilities are simplifying compliance, saving time, and improving safety
- Real-world success stories from customers who made the switch
Whether you’re managing one site or two hundred, APSM helps you keep everything organized, visible, and audit-ready — without the stress.
On March 1, 2024, the EPA finalized and released the Safer Communities by Chemical Accident Prevention Rule (SCCAP), which amends the Risk Management Program that will require each Program 2 and Program 3 facility to update their program. The final rule will take effect 60 days after publication in the Federal Register.
The EPA released a fact sheet that includes a helpful summary of the changes, which can be found here. EPA SCCAP Fact Sheet
Prevention Program (Subparts C and D)
- Natural hazards and power loss: (1) Adding amplifying regulatory text to emphasize that natural hazards (including those that result from climate change) and loss of power are among the hazards that must be addressed in Program 2 hazard reviews and Program 3 process hazard analyses. (2) Requiring back-up power for release monitoring equipment. (3) Requiring a justification in the Risk Management Plan when hazard evaluation recommendations are not adopted.
- Facility siting: (1) Emphasizing that facility siting should be addressed in hazard reviews and explicitly defining the facility siting requirement for Program 2 hazard reviews and Program 3 process hazard analyses. (2) Requiring a justification in the Risk Management Plan when facility siting hazard recommendations are not adopted.
- Safer technologies and alternatives analysis: Requiring (1) A STAA evaluation for all Program 3 NAICS 324 and 325 processes; (2) A Practicability assessment of inherently safer technologies and designs (IST/ISD) considered for processes (a) in Program 3 NAICS code 324 and 325 within one mile of another Program 3 NAICS code 324 or 325 process, (b) with hydrofluoric acid alkylation processes classified under NAICS 324, (c) having one RMP accident since the facility’s most recent process hazard analysis; (3) Implementation of at least one passive measure at the facility, or IST/ISD, or a combination of active and procedural measures equivalent to or greater than the risk reduction of a passive measure for the same facilities required to conduct the practicability assessment and (4) A justification in the Risk Management Plan when STAA recommendations are not adopted.
- The STAA provision ONLY applies to Program 3 NAICS 324 and 325.
- Root cause analysis: Requiring a formal root cause analysis incident investigation when facilities have had an RMP-reportable accident.
- Third-party compliance audits: (1) Requiring the next scheduled compliance audit be a third-party audit when facilities have had an RMP-reportable accident. (2) Requiring a justification in the Risk Management Plan when third-party compliance audit recommendations are not adopted.
- Employee Participation: (1) Requiring employee participation in resolving process hazard analyses, compliance audit and incident investigation recommendations and findings. (2) Outlining stop work procedures in Program 3 employee participation plans. (3) Requiring Program 2 and Program 3 employee participation plans to include opportunities for employees to anonymously report RMP-reportable accidents or other related RMP non-compliance issues. (4) Requiring training on employee participation plans.
Emergency Response (Subpart E)
- Community notification of RMP accidents: (1) Requiring non-responding RMP facilities to develop procedures for informing the public about accidental releases. (2) Requiring release notification data be provided to local responders. (3) Partnering with local responders to ensure a community notification system is in place for notification of RMP-reportable accidents.
- Emergency response exercises: (1) Requiring a 10-year frequency for field exercises unless local responders indicate that frequency is infeasible. (2) Requiring mandatory scope and reporting requirements for emergency response exercises.
Information Availability (Subpart H, 68.210)
- Enhanced Information Availability: New requirements for the facility to provide chemical hazard information upon request to the public living, working or spending significant time within six miles of the facility, in at least two most common languages in the community. Under the previous regulation, facilities were not required to provide this information.
Other Areas of Technical Clarification (Subparts A, C, D)
Minor regulatory edits to clarify:
- Program 3 process safety information should be kept up to date,
- Program 2 and Program 3 requirements consistent for recognized and generally accepted good engineering practices (RAGAGEP),
- Hot work permits should be retained for three years,
- Fiscal or calendar prior year sales should be used to qualify for the retail facility exemption,
- RAGAGEP should be reviewed in process hazard analyses to determine gaps in safety.
What are the final compliance dates for the changes?
EPA is requiring regulated sources to comply with:
- New STAA, incident investigation root cause analysis, third-party compliance audit, employee participation, emergency response public notification, exercise evaluation reports, and information availability provisions, three years after the effective date of the final rule.
- Revised emergency response field exercise frequency provision by March 15, 2027, or within 10 years of the date of an emergency response field exercise conducted between March 15, 2017, and August 31, 2022.
- Updates and resubmission of risk management plans with new and revised data elements, four years after the effective date of the final rule.

Workplace safety and compliance isn’t just about following rules or sitting in boring certification meetings. It’s about fostering an environment where safety is ingrained in every aspect of your organization and making sure that every employee is empowered to play their part. If you’ve Googled workplace safety and compliance culture to find this page, keep reading for helpful insight on building a compliance culture gathered from our 30 years in Process Safety Management
Compliance Culture Definition
Diligent.com describes creating a culture of compliance as “embedding good behaviors at all levels of your organization. It means helping people to make better decisions in following your business’s rules, regulations and policies”. This is the typical baseline used by most organizations to ensure employees are making decisions that reflect the company’s values and “do no harm” to others.
When we talk about safety and regulatory compliance, this definition is foundationally correct. But as OSHA confirms, to ensure safe and healthy workspaces, we need to step further:
Top-performing workplace safety and health programs start with developing and fostering communication between management and employees. These workplaces always strive to improve. They share information about best safety and health practices, integrate new or innovative solutions to an otherwise unsafe task and benchmark with other employers in their respective industries.
Michelle Ellison, Indiana Assistant Commissioner of Labor, Indiana Occupational Safety and Health Administration
In this guide, we’ll cover three pillars of building a compliance culture: leadership, communication, and resources, plus simple, actionable tips for establishing each. Then, we’ll discuss tips for managing change, and tools, like PSM software that help streamline the process.
Leadership’s Role in Safety & Compliance
A safety culture starts and ends with leadership. If the bosses don’t take it seriously, why should anyone else? Here’s how leaders can truly drive safety:
Wak the talk: Leaders should be the poster children of safety. If they’re bypassing protocols, everyone else will too. Consistency is key.
Set clear, actionable goals: Vague goals help no one. Be specific about what you want to achieve regarding safety and compliance, and let everyone know what’s expected.
Provide Resources: It’s one thing to talk about safety, but another to back it up with the right tools and training. Make sure your team has everything they need to stay safe.
Leadership is a crucial component of a strong safety culture. A leader’s attitude towards safety trickles down to every level of the organization. Lead by example, and you’ll see a ripple effect of safety consciousness throughout your company.
Effective Compliance Communication
In the safety world, communication is king. Keeping everyone in the loop and making sure safety is a constant conversation is what it’s all about. Here’s how:
Regular Safety Meetings and Updates: Don’t let safety be an afterthought. Regular meetings keep it front and center.
Visible Safety Reminders: Posters, signs, digital displays – use them all to keep safety messages visible.
Create Open Channels for Feedback: Make it easy for anyone to voice their safety concerns or ideas. An open-door policy can do wonders.
Regular communication reinforces the importance of safety and compliance from a regulatory perspective, but the repetition also ensures that these communications become ingrained in your company culture. When everyone is aware of their role and understands their responsibility in maintaining a strong compliance culture, it becomes easier to weave safe practices into every facet of work.
Safety Training & Resources
Knowledge and tools – that’s what your team needs to tackle safety head-on. Here’s how to make sure they’re well-equipped:
Tailored Training Programs: Generic training just doesn’t cut it. Customize your training to fit the specific needs of different roles in your organization.
Continuous Learning Opportunities: Safety isn’t a one-and-done deal. Keep your team’s knowledge fresh with regular workshops and refresher courses.
Invest in Proper Safety Equipment: And make sure everyone knows how to use it. Having the right tools can be the difference between a close call and a catastrophe.
Well-trained and well-equipped teams are your first line of defense against accidents. Invest in your team’s safety skills, and you’re investing in your organization’s future.
Stay Alert: How to Foster a Compliance Culture
Just like calm seas don’t make skilled sailors, a smooth-running workplace can sometimes lead to a relaxed approach to safety. But remember, it’s in those calm moments that your team’s preparedness really counts. Here are ways to ensure your team stays alert and ready for anything:
Conduct regular safety drills: Are safety drills part of your strategic compliance plan? If not, consider scheduling them like you would any other compliance metric, like recertification or mandatory training sessions. It’s a great way to keep everyone alert and ensures that, in case of an actual emergency, your team will be ready to respond.
Discuss near-misses: Set up a ‘lessons learned’ forum that allows team members to share experiences and learn from close calls without fear of being judged. Transparency turns every near-miss into a valuable lesson and may uncover important questions or stumbling blocks that you can address.
Incentivize safety: How about a safety suggestion box or a monthly safety challenge? Give recognition to innovative safety ideas and practices. It’s a great way to keep everyone engaged and thinking proactively about safety.
Incorporating these strategies matters because they foster a culture of continuous alertness and learning. By adopting these practices, your organization can not only prevent incidents but also build a more knowledgeable and safety-conscious team. The key takeaway? Start implementing these changes today, and watch your safety culture transform.
The Role of Compliance Software in Enhancing Workplace Safety
As we navigate the complexities of creating a robust safety culture, the role of compliance software tools becomes increasingly significant. These platforms offer much more than just a way to adhere to regulations; they provide a comprehensive system for enhancing and managing safety culture:
Compliance Software Tools: These tools streamline the process of managing safety and regulatory compliance, creating an integrated system that supports every aspect of your organization’s safety culture.
Compliance Software Platforms: Such platforms transform traditional safety approaches, fostering proactive participation from employees and enabling real-time safety monitoring and incident reporting.
PSM Compliance Software: Specifically designed for process safety management, this software tackles unique industry challenges, offering tools for risk analysis and performance tracking to maintain high safety standards.
These compliance management systems are instrumental in changing and improving safety culture in the workplace. They not only help in overcoming compliance challenges but also play a crucial role in making safety a natural part of your organization’s workflow.
Tips For Embracing Change
Who likes change? Not many, but in the world of safety, it’s your best friend. It’s all about evolving and getting better at keeping everyone safe. Here’s how to get your team on board with changes:
Clearly communicate why change is occurring: Use real-life examples to show how new safety measures have made a difference. It’s not about change for the sake of it; it’s about making everyone’s job safer.
Involve your team in the process: When people have a say in the changes being made, they’re more likely to buy into them. Set up brainstorming sessions, let everyone throw in their two cents, and watch the buy-in grow.
Celebrate adoption: Change isn’t easy, so when your team gets it right, make a big deal about it. A little recognition goes a long way in reinforcing positive shifts.
Taking steps like these transforms the perception of change from another silly “to-do” into an opportunity for improvement. Shifting that mindset is one part of the journey to a safer workplace.
Stay Consistent
Consistency is the name of the game in safety. It’s about ensuring everyone’s on the same page, no matter where they are in the organization. Here’s how to keep things uniform and effective:
Standardize Safety Protocols: One set of rules for all. Make sure every department and location follows the same safety guidelines.
Conduct Regular Audits: Keep everyone honest and on track with frequent safety audits. It’s like a health check for your safety practices.
Address Non-Compliance Constructively: When someone strays from the path, use it as a teaching moment rather than a blame game.
Consistency matters because it eliminates confusion and sets a clear expectation for everyone. Uniformity in safety practices ensures everyone is working towards the same goal of a safe workplace.
Focus on Continuous Improvement
The world changes, and so should your safety strategies. Staying ahead means always looking for ways to do things better. Here’s your game plan:
Actively seek feedback: Sometimes, the best safety ideas come from the front line. Encourage your team to share their thoughts and experiences.
Analyze incidents for insights: Every incident, big or small, is a learning opportunity. Dive deep into what happened and why, and use those insights to improve.
Be ready to adapt: When you find a better way to do things, don’t hesitate to make changes. Flexibility is key to staying safe.
Continuous improvement is so important! It ensures that your safety practices evolve with changing conditions and new information. Never stop looking for ways to enhance your safety culture.
Compliance Culture FAQs
Why is compliance so important?
Compliance isn’t just about following laws; it’s about creating a safe, efficient, and ethical work environment. It protects your employees, your reputation, and your bottom line.
What are the benefits of an effective compliance program?
A robust compliance program minimizes risks, boosts employee morale, and enhances brand reputation. It’s the backbone of a trustworthy and reliable organization.
What is the impact of non-compliance on an organization?
Non-compliance can lead to legal troubles, financial losses, and a damaged reputation. It’s a risk no organization should take.
How is process safety management (PSM) software useful?
PSM software streamlines safety processes, ensures regulatory compliance, and helps identify potential hazards before they turn into real problems. It’s a critical tool in your safety arsenal.
Conclusion
Building a strong safety culture takes time, effort, and dedication, but it’s one of the best investments you can make. Implement these strategies today, and you’ll create an environment where safety is a natural part of the workflow.
APSM’s tools and expertise help a vast array of organizations—from pharmaceuticals to oil & gas—begin the process of changing safety culture. Our Catalyst Portal, along with software for compliance management and comprehensive training, can help transform your approach to safety and compliance. To learn more about APSM’s offerings and create a tailored safety and compliance strategy for your team, reach out to us at info@apsm.net or call 833-411-APSM for a consultation.
Compliance specialists and HR teams responsible for managing compliance and safety certifications know that regulations are ever-evolving. In the hectic day-to-day, it’s easy to think of safety and compliance as an annoying “to-do” or a box to check. While being reactive might work in the short term, all too soon, you’ll be scrambling to catch up. Instead of risking facility safety and regulatory fines, it’s important to make regulatory compliance part of your strategic plan.
One way to do this? By establishing a strong culture of compliance. Instead of checking off a to-list that keeps the company safe (a very important thing!), compliance culture focuses on the employee and ensures that everyone on the team—from senior leadership down—is adopting a safety and compliance-first mentality in every aspect of the organization. This blog post delves into comprehensive strategies and practical steps for cultivating a robust compliance culture.
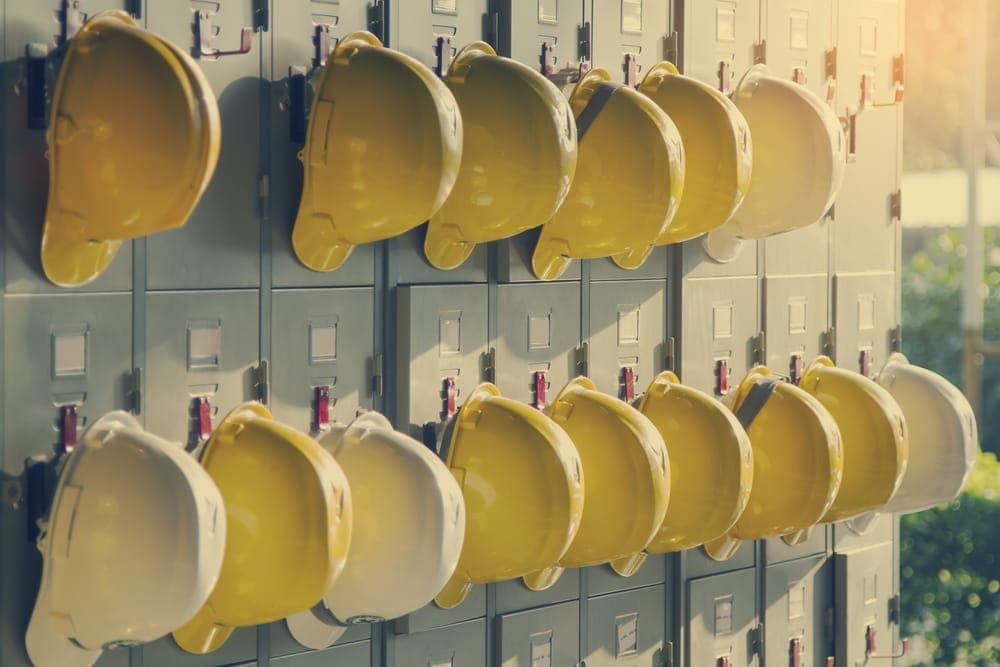
Process Safety Management
Before we talk about creating a culture of safety and regulatory compliance at work, it’s important to know why it might be necessary. First, when we talk about safety and regulatory compliance, we’re not just talking about the basics. Typically, this level of compliance goes hand in hand with process safety management (PSM).
What is PSM?
When you think about process safety management (PSM) you might have a good idea of the general outline: it’s required by OSHA for any US employer with a process that involves specific hazardous and/or flammable chemicals in quantities above 10,000 pounds. Per OSHA, “PSM is a “performance-based” standard that outlines key features of safety programs for controlling highly hazardous chemicals. Employers have the flexibility to tailor their safety programs to the unique conditions at their facilities.”
PSM Key Features
OSHA Process Safety Management Standard
OSHA’s PSM standard (OSHA 29 CFR 1910.119) lists the key features of an acceptable safety program that industries including refining, pharmaceuticals, oil and gas, must implement, including:
- Compliance Audits: Regularly auditing your processes and procedures to ensure ongoing compliance with safety regulations and standards.
- Training: Providing comprehensive training for all employees on operational procedures, safety practices, and emergency response.
- Process Safety Information: Maintaining detailed records of all hazardous chemicals used, including their properties and handling procedures.
- Incident Investigation: Promptly investigating any safety incident to understand its cause and take steps to prevent future occurrences.
- Management of Change: Managing changes in processes, equipment, or personnel with a structured approach to assess safety impacts and necessary modifications.
- Hot Work Permits: Issuing permits for any hot work activities, like welding or cutting, to ensure safety measures are in place and risks are assessed.
- Operating Procedures: Developing clear, written instructions for safely conducting each process, including startup, shutdown, and emergency operations.
- Trade Secrets: Balancing the protection of trade secrets with the need to disclose enough information to ensure the safety of your processes and employees.
- Mechanical Integrity: Regularly inspecting and maintaining critical equipment to prevent failures and ensure safe operation.
- Emergency Planning and Response: Developing and regularly updating emergency response plans for potential incidents, including evacuation procedures and first aid measures.
- Employee Participation: Involving your team in regular safety discussions and encouraging them to report potential hazards or suggest improvements.
- Process Hazard Analysis: Conducting thorough analyses to identify potential risks in your processes and determining necessary precautions or modifications.
- Pre-startup Safety Review: Performing a safety review before starting any new or modified process to ensure all safety systems are functional.
- Contractors: Ensuring that contractors working on-site are informed about your company’s safety policies and procedures and understand their role in maintaining a safe environment.
Now that we’ve covered the essentials of Process Safety Management (PSM), it’s time to delve into practical ways to incorporate safety and compliance into your company’s daily operations.
Getting Ahead of Regulatory Changes in Safety & Compliance
First, a hard truth: regulations change frequently and without warning. To stay ahead, organizations must develop proactive systems for monitoring updates. This includes subscribing to regulatory news feeds, attending industry conferences, and engaging in professional networks. Integrating regulatory updates into daily operations requires a systematic approach. Regular training sessions, updates to operational manuals, and open forums for discussion are essential to ensuring that your entire team is aware and informed. Additionally, these efforts go a long way toward ensuring that every team member, from the front-line staff to the executive suite, understands the implications of these changes. Understanding ‘why’ something is necessary is crucial for achieving the buy-in necessary to drive compliance.
To keep your organization up-to-date regarding safety and compliance without spending hours manually scheduling training sessions, updating OSHA binders, and chasing news alerts, consider implementing compliance software. PSM software like APSM can streamline your workflow by tracking real-time alerts and updates, keeping you informed of the latest regulatory developments, and enabling you to plan for the future. Centralizing updates and changes with a software solution makes the process of tracking implementation straightforward, which can also go a long way toward aligning departments and teams.
Schedule a Demo with us!
Creating a Culture of Safety & Compliance
Adopt a Structured Approach
The complexity of modern safety and compliance requirements can be daunting. To simplify, break down regulations into manageable, actionable steps. Use flowcharts, decision trees, and checklists to demystify complex regulations. APSM’s software aids in this simplification by providing structured templates and compliance checklists, ensuring that every regulatory requirement is addressed systematically.
Make Attention to Detail the Norm
Cultivating meticulousness in compliance-related tasks is vital. Regular internal audits, surprise checks, and feedback sessions contribute to a culture where attention to detail is paramount. Recognition programs for teams and individuals who demonstrate exemplary compliance practices can further encourage this mindset.
Prioritize and Delegate Tasks
Efficient compliance management involves smart prioritization and delegation. Identify tasks that are time-intensive and evaluate if they can be automated, streamlined, or delegated. Training and empowering team members to handle delegated tasks ensures that compliance processes are both efficient and effective.
Automate Manual Processes
The automation of compliance processes is a game-changer. It frees up valuable time and resources, allowing teams to focus on strategic aspects of compliance. APSM’s software shines in this domain, automating document management, deadline tracking, and even certain aspects of reporting. This automation transforms cumbersome, manual tasks into efficient, streamlined processes.
Aligning the Team For Safety & Compliance
Encourage Cross-Departmental Collaboration
One of the greatest challenges in compliance is ensuring cross-departmental synergy. Regular interdepartmental meetings, joint training sessions, and a unified compliance platform can significantly reduce the gaps. APSM’s software facilitates this synergy by providing a platform where different departments can collaborate, share information, and track collective progress. In addition, strive for clarity: clearly defining the roles and responsibilities of each department and team is crucial for effective compliance management. Clearly defined roles prevent overlaps and gaps in compliance efforts.
Offer Specialization and Continuous Learning
Every initiative needs champions—why not encourage your employees to lead the charge? In the realm of compliance, continuous learning is not optional; it’s essential. Encourage your team to engage in ongoing education, whether through online courses, workshops, or industry seminars. Specialization in particular areas of compliance can bring depth to your team’s expertise.
Leverage External Expertise
Sometimes, external expertise can provide the impetus needed for advanced compliance management. Engaging consultants, attending industry workshops, and utilizing resources from regulatory bodies can provide fresh perspectives and specialized knowledge. APSM’s network of experts and comprehensive resources can be particularly valuable in this regard.
Fostering Proactive Compliance
Plan For the Future
forward-thinking compliance strategy is one that anticipates future trends and regulatory shifts. This involves keeping an eye on regulatory discussions, industry trends, and technological advancements. APSM’s predictive analytics and trend monitoring can be instrumental in this proactive stance, helping you stay one step ahead.
Build a Corporate Safety & Compliance Strategy
For compliance to be truly effective, it must be woven into the fabric of the organization’s strategic planning. This means aligning compliance goals with business objectives and ensuring that compliance considerations are part of every major decision. APSM’s strategic planning tools can help integrate compliance seamlessly into your business strategy.
Cultivating a Safety & Compliance-Conscious Culture
Generating Leadership Buy-In
Leadership commitment to compliance sets the tone for the entire organization. Leaders who prioritize compliance in their actions and decisions send a powerful message about its importance. Regular communication from leadership about the value and necessity of compliance further reinforces this culture.
Communicating the ‘Why’ Behind Safety & Compliance
Understanding the ‘why’ behind compliance is as important as knowing the ‘what’ and the ‘how.’ Employees who understand the reasons behind compliance measures – be it ethical, legal, or business-related – are more likely to embrace these practices. Educational campaigns, storytelling, and case studies can be effective in communicating this message.
Measuring and Celebrating Safety & Compliance Success
Track Safety & Compliance Metrics
What gets measured gets managed. Regular tracking of compliance metrics not only helps in identifying areas for improvement but also provides opportunities to celebrate successes. Metrics such as the number of compliance incidents, audit results, and training completion rates offer valuable insights into the health of your compliance culture. APSM’s software offers robust tools for tracking these metrics, providing a clear picture of your compliance landscape.
Create a Culture of Recognition
A culture that recognizes and celebrates compliance achievements fosters a positive compliance environment. Acknowledgment in company meetings, newsletters, or formal awards can motivate teams and individuals to maintain high compliance standards.
The Best PSM Software
What To Look For & How to Choose
In the journey towards a robust compliance culture, APSM’s suite of tools and expertise acts as a powerful ally. By addressing the multifaceted aspects of compliance – from keeping abreast of regulatory changes to streamlining complex compliance processes – APSM’s software empowers organizations to navigate the compliance landscape confidently. The software’s capabilities in automating time-consuming tasks, enabling cross-departmental collaboration, and offering strategic insights make it an indispensable tool for any organization committed to strengthening its compliance culture.
Conclusion
Building a culture of compliance is an ongoing endeavor, demanding constant vigilance, adaptation, and a proactive approach. By implementing these advanced strategies and leveraging APSM’s comprehensive solutions, safety and compliance professionals can ensure their organizations are not only compliant with current standards but also well-prepared to meet future challenges.
Let APSM’s software and expertise strengthen your compliance strategies, paving the way for a safer, more compliant future. Reach out to us at info@apsm.net or call 833-411-APSM for a consultation.
We at APSM hope this blog post finds you well and that your PSM compliance efforts are running smoothly. At APSM, we are committed to continuously enhancing our software to better serve your needs. To keep you informed about the latest updates, industry insights, and helpful resources, we invite you to follow APSM on LinkedIn.
Stay Informed with Software Updates
LinkedIn provides an excellent platform for us to share important software updates and enhancements directly with you. By following APSM on LinkedIn, you will:
- Receive timely notifications about new features and enhancements in our software, ensuring that you stay up-to-date with the latest improvements.
- Gain insights into how these updates can optimize your PSM compliance processes, improve efficiency, and enhance overall productivity.
- Learn about upcoming releases, beta programs, and opportunities to provide feedback on new features, allowing you to actively shape the future of APSM software.
Join APSM on LinkedIn today to stay informed, connected, and inspired!
How to Follow APSM on LinkedIn
Following APSM on LinkedIn is easy:
1. Visit our APSM LinkedIn page at https://www.linkedin.com/company/apsm/.
2. Click the “Follow” button on our LinkedIn page to start receiving our updates in your LinkedIn feed.
3. Engage with our content by liking, commenting, and sharing to join the conversation and expand your network.
We are excited to connect with you on LinkedIn and provide you with valuable software updates, industry insights, and resources to support your PSM compliance journey. Should you have any questions or require assistance, our dedicated support team is always available at info@apsm.net.
We’ve added a new permission to the APSM Portal that governs access to the Certification of Incident Investigation Management Reviews. Before this update, any user with Plant Administration or Multi/Company Administration permissions could Certify the Management Review of an Incident Investigation. Now you can specify which users with Plant Administrator + permissions can Certify Management Reviews by giving them the Management Review permission. No other user, administrator or otherwise, can Certify a Management Review without this permission. Users given this permission will also notice they have a new dashboard object (Inc Inv Mgmt. Review) displaying incidents that have been reviewed and need to be certified.
NOTE: If no one has Management Review permissions for a Plant, all Plant or Multi/Company Administrators will still be able to Certify Incident Investigation Management Reviews. By giving a user/users the Management Review permission for a Plant, you are locking it down to those users.
The following is a step-by-step tutorial on how to give the Management Review permission to specific users.
Setting the Management Review Permission
Users with Company Administration + permissions can manage Incident Investigation Notification settings for Plant(s) they have access to.
- Within the Online Incident Investigations Grid, select the Incident Investigation Notifications Button.
- This opens the Incident Investigation Notifications grid. If the user is not listed, select the Add Button.
- This opens the Add / Edit Incident Investigation Notification window. Select an employee from the Person to Notify dropdown, check the Management Review option, and select Save.
- If the user is already listed, select the Edit Button to the right of their name.
- Check the Management Review option and select Save.
Inc Inv Mgmt Dashboard
Giving a user the Management Review permission will activate the Inc Inv Mgmt Review Dashboard object.
Note: The Inc Inv Mgmt Review Dashboard object is only visible when there are Incident Investigations being reviewed.
Why Earn Your Certification?
The benefits of earning your certification are invaluable:
Management
Improve Productivity:
Proper training and certification improves productivity by a factor of 4x
Faster Return on Investment:
Ensure that you are utilizing all of the available APSM software capabilities within your organization
Partners
Differentiation:
Customers look for APSM certification when selecting partners to work with
Quality and Reliability:
APSM certifications ensure a partner will be able to deliver value across all APSM solutions with high quality and efficiency
If you aren’t sure which level of certification is right for you, below is a detailed review of each of the levels.
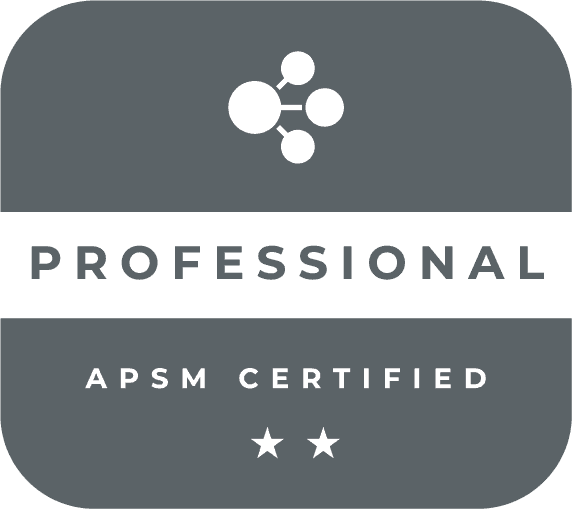
Certified Professional
This is our standard level of recognition and is designed to verify all the required skill to implement, operate, maintain, troubleshoot, and support the APSM software suite from a typical or standard user view. This is the certificate recommended for plant and company administrators. Cost is $1,295
The Professional level certification is valid for a period of two (2) years.
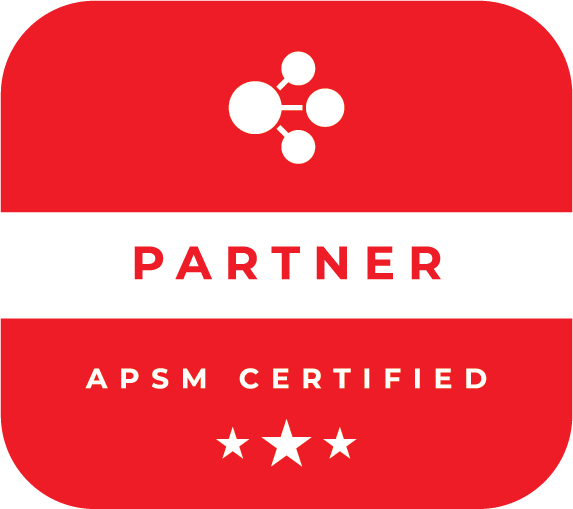
Certified Partner
The APSM Partner certification is our highest level of recognition and provides to create and manage multiple plant or company installations and verifies the highest level of expertise in system configuration, program and facility implementation, operations, maintenance, training, troubleshooting, technical support, and demonstrates complete competency and support of the APSM Software suite. This is the certificate recommended for multi-company administrators, contractors, and consultants with responsibility for multiple companies and multiple plant locations. Cost is $1,995
The Partner level certification is valid for a period of two (2) years.
As of right now, there are 6 different dates and locations to choose from. Each of the options will offer the same levels of certification (professional and partner).
Area |
Location |
Dates |
Central |
Dallas, TX |
Jan. 10-12 |
Pacific NW |
Pasco, WA |
April 18-20 |
Southeast |
Atlanta, GA |
May 9-11 |
Midwest |
Minneapolis, MN |
July 25-27 |
Central* |
St. Louis, MO |
Sep. 12-15* |
West |
Salt Lake City, UT |
Oct. 10-12 |
* This class is a 4-day option that will also be focused on the new Catalyst software tools.
To sign up for any location or class, or to request additional information, please click below to fill out a form!
Sign Up for Training Today!Announcing Additional Multi-Facility Tools
APSM is excited to announce some major updates to user permissions within the APSM Portal – especially helpful for multi company users and Contractors. In the past, users needed Plant Administrator permissions to access multiple Plants/Locations. Now normal users can be given access to multiple Plants/Locations without needing Plant Admin permissions.
Also, Administrators can now set specific permissions for users at different locations and users can be assigned SOP Training at multiple Plants/Locations (this used to be limited to their home plant).
- Normal Users Access Multiple Plants/Locations
- Users can be granted specific Permissions per Plant/Location
- Users can be assigned SOP Training at multiple Plants/Locations
- Users can take SOP Training for multiple Plants/Locations from Dashboard
Normal Users Access to Multiple Plants/Locations
Now, normal users that belong to multiple Plants/Locations can access and switch plants using the drop-down menu at the top of the page.
- Select the drop-down menu at the top of the page and select one of the available locations.
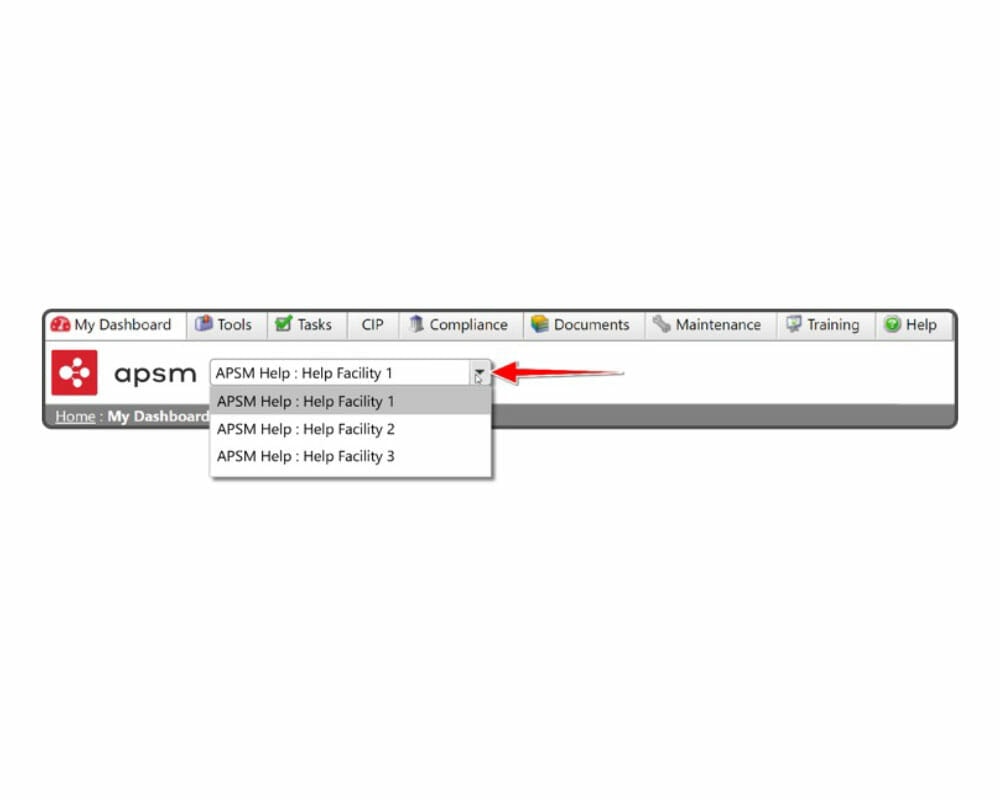
Users can be granted specific Permissions per Plant/Location
Administrators can edit which Plants/Locations users can access by selecting the “Belongs to Plants/Locations” link within a user’s Edit Employee page. Administrators can also give users specific permission levels for each Plant/Location.
For example, if a user is an administrator for Plant A and you want to give them access to Plant B — but don’t want them to be able to delete anything in Plant B — you can assign them Normal User permissions for Plant B.
- Select the Belongs to Plants/Locations link
- Select the Plant/Location you want to give access to and change the Permission Type
- Select Save Changes.
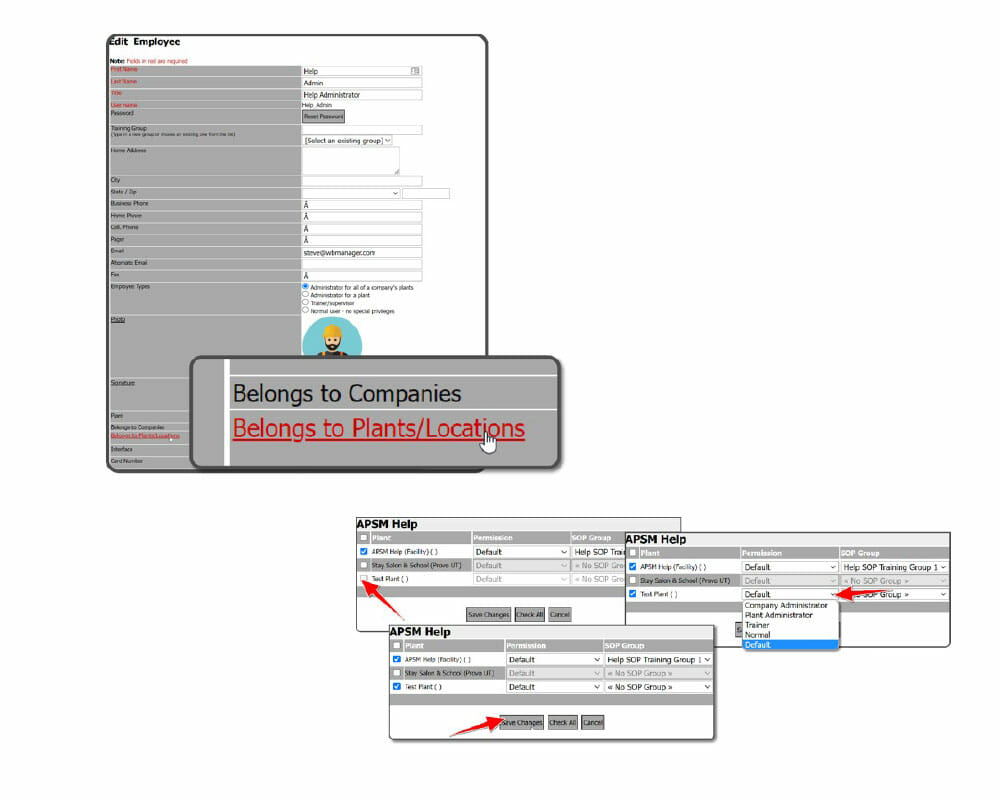
Users can be assigned SOP Training at multiple Plants/Locations
Administrators can use the Belongs to Plants/Locations link to assign users an SOP Training Group per Plant/Location. Administrators can also make the SOP Training Group assignment using the specific plant’s SOP Training Administration Group Manager.
Users will appear on reports and count toward plant scorecards for any location they are assigned an SOP Training Group. A user’s dashboard will display SOP Training assignments for each affiliated Plant/Location.
Employee Edit Page
- Select the Belongs to Plants/Locations link.
- Select the Plant/Location you want to Assign SOP Training to and change the SOP Group
- Select Save Changes
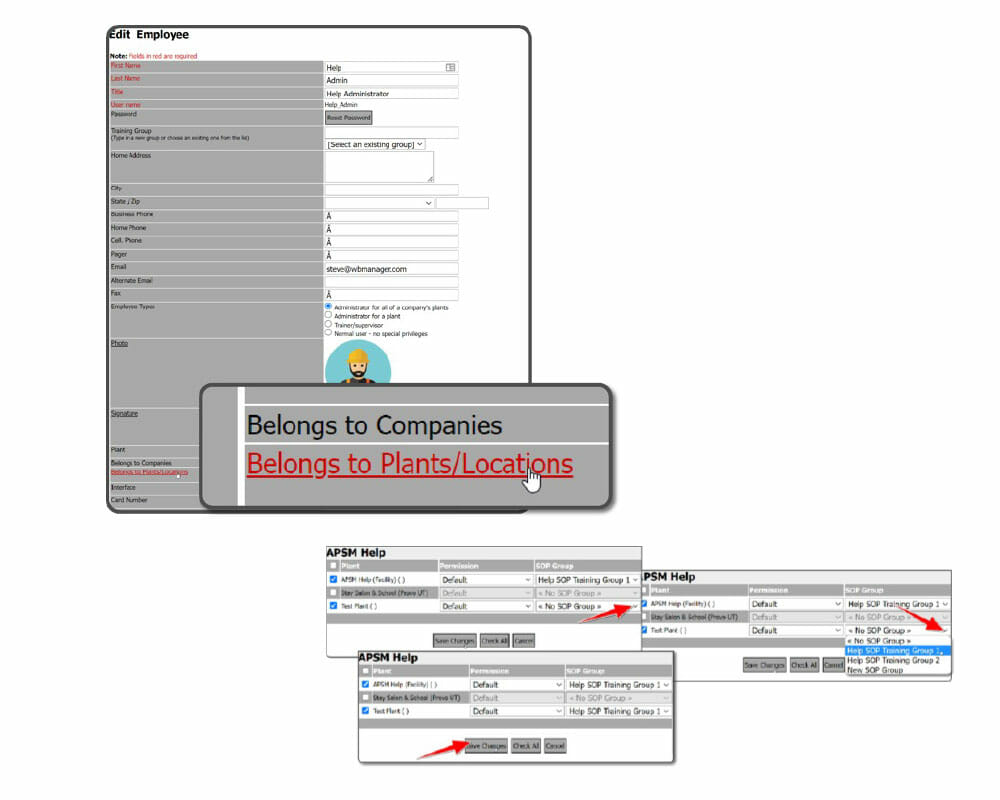
SOP Training Administration > Group Manager Page
- Select Training, then Administration, then SOP Training Administration, then Group Manager.
- Select the Group from the list on the left you want to assign the User to and select the Add button next to the Employee
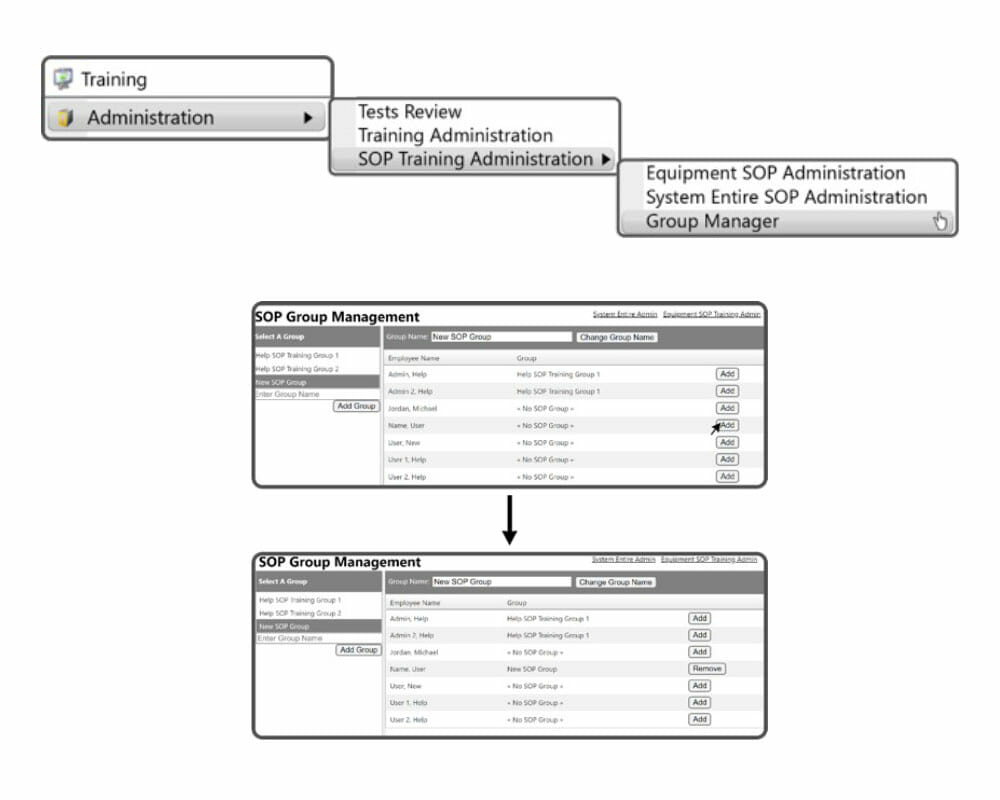
Users can take SOP Training for multiple Plants/Locations from Dashboard
Users can view and take their assigned SOP Training (for multiple Plants/Locations) in the Training section of the Dashboard. The grid now has a Plant/Location Column/Filter.
*Please note that if accessing Training thru the menu via Training > SOP Training, that is controlled by the Plant you are currently in.
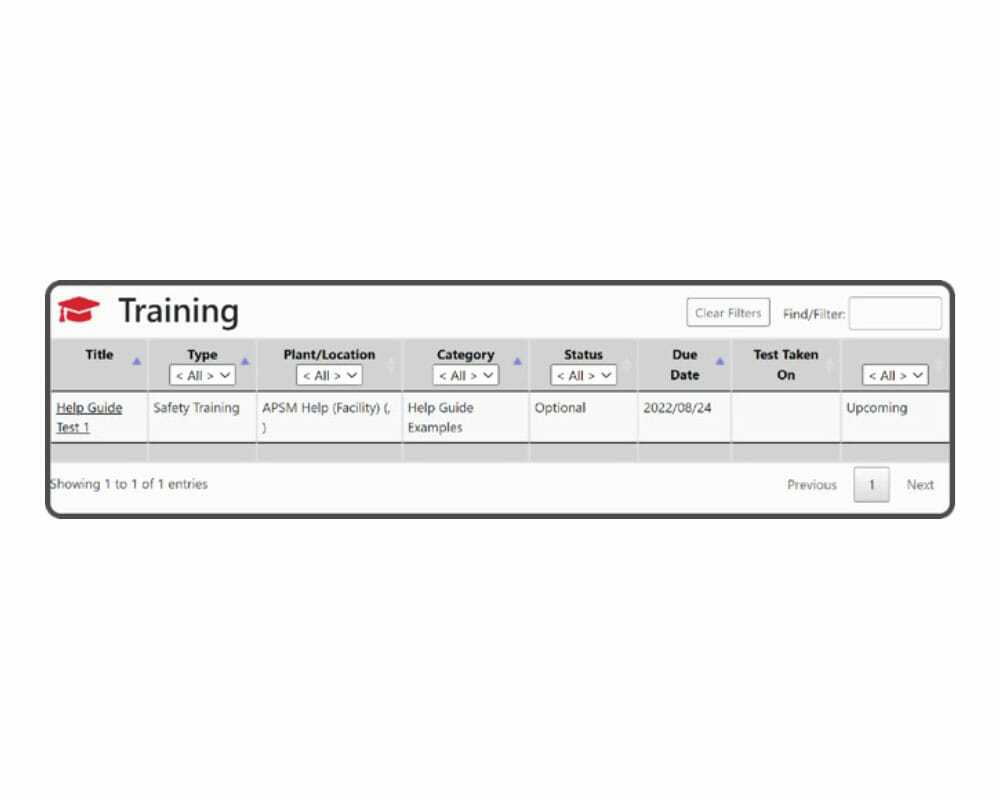
Announcing Two Updates to the APSM Certification Training Schedule
APSM has added another class option (Boston area in October) and modified the date of the South class (now in January ‘23) for the Certification Training Schedule. The APSM Certification program offers participants credentials through certification and testing in order to recognize depth in competency and expertise in the APSM software suite.
Why Earn Your Certification?
The benefits of earning your certification are invaluable:
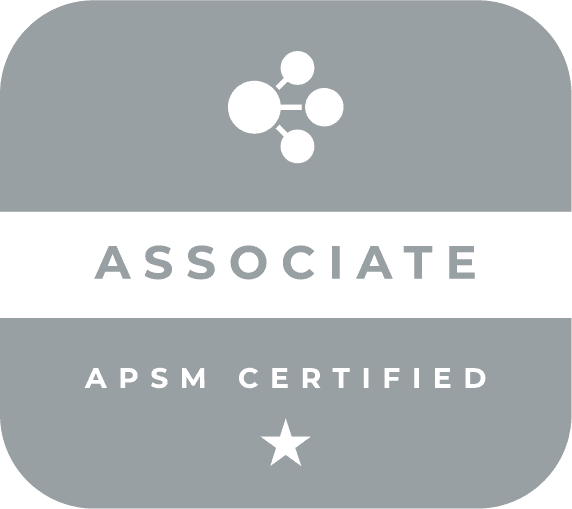
Individuals
Grow Your Career:
Accelerate your professional development
Build a Reputation:
Enhance your credibility as an expert and increase your value as an employee
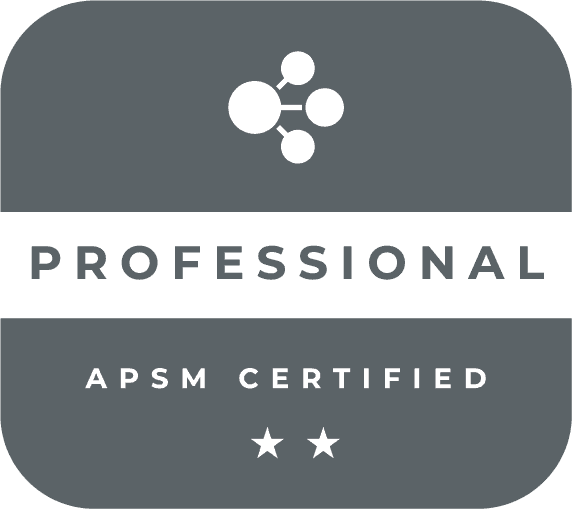
Management
Improve Productivity:
Proper training and certification improves productivity by a factor of 4x
Faster Return on Investment:
Ensure that you are utilizing all of the available APSM software capabilities within your organization
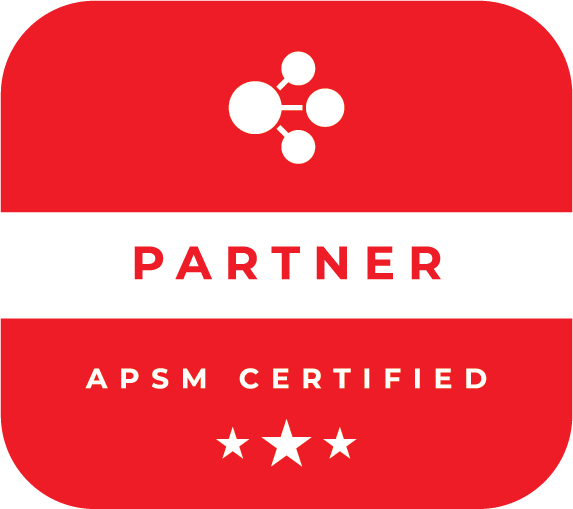
Partners
Differentiation:
Customers look for APSM certification when selecting partners to work with
Quality and Reliability:
APSM certifications ensure a partner will be able to deliver value across all APSM solutions with high quality and efficiency
If you aren’t sure which level of certification is right for you, below is a detailed review of each of the 3 levels.
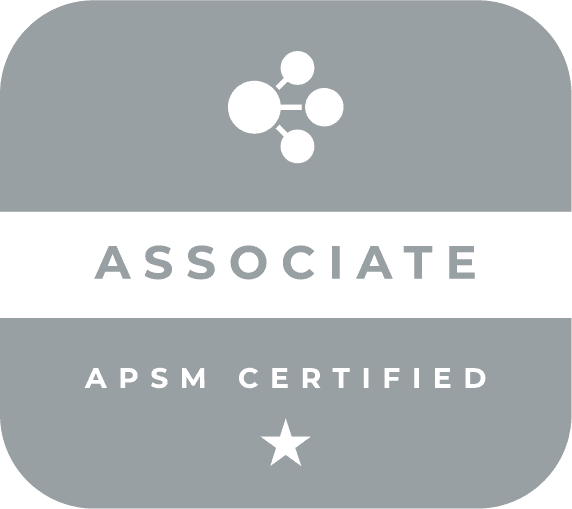
Certified Associate
This is our first level of recognition and is designed to provide you with the knowledge and skills needed to navigate, implement, and utilize the APSM software suite. This is the certificate recommended for plant administrators or coordinators with responsibility for one plant location. Cost is $995
The Associate level certification is valid for a period of three (3) years.
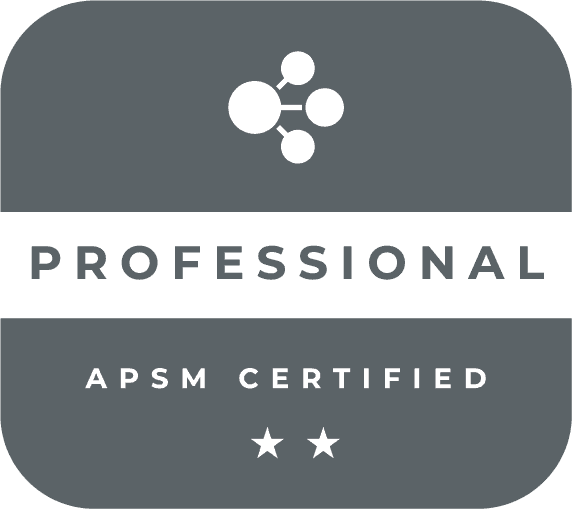
Certified Professional
This is our second level of recognition and is designed to verify all the required skill to implement, operate, maintain, troubleshoot, and support the APSM software suite from a multi-facility view. This is the certificate recommended for company administrators or corporate coordinators with responsibility for multiple plant locations. Cost is $1,495
The Professional level certification is valid for a period of two (2) years.
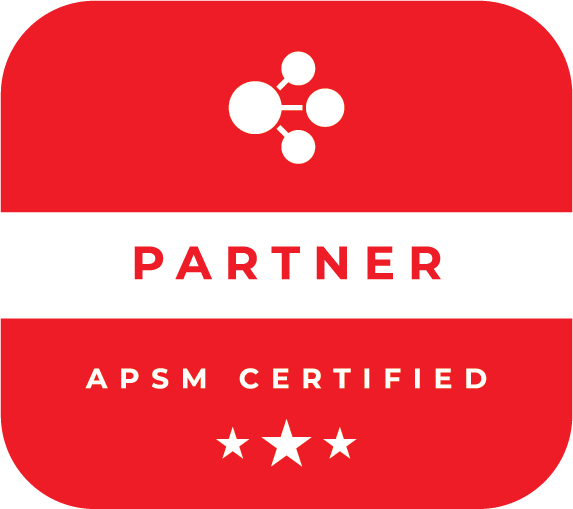
Certified Partner
The APSM Partner certification is our highest level of recognition and provides to create and manage multiple plant or company installations and verifies the highest level of expertise in system configuration, program and facility implementation, operations, maintenance, training, troubleshooting, technical support, and demonstrates complete competency and support of the APSM Software suite. This is the certificate recommended for multi-company administrators or contractors with responsibility for multiple companies and multiple plant locations. Cost is $1,995
The Partner level certification is valid for a period of two (2) years.
As of right now, there are still 5 different dates and locations to choose from. Each of the options will offer the same 3 levels of certification (associate, professional, and partner).
Area |
Location |
Dates |
Southeast |
Atlanta, GA |
June 14–17 |
Midwest |
Appleton, WI |
Aug. 16–19 |
APSM Office |
Orem, UT |
Sept. 27–30 |
Northeast |
Boston, MA |
Oct. 19-21 |
South |
Dallas, TX |
Jan. 10-13 (2023) |
To sign up for any location or class, or to request additional information, please click below to fill out the form!
Sign Up for Training Today!*Please note that each of these training classes will comply with the local COVID guidance. Details will be provided to all attendees of each particular session.